Выбор ножа – это не только вопрос формы клинка и его предназначения, но и вопрос качества стали и обработки, которой он подвергается. Финишная обработка влияет на его внешний вид, а также на такие важные характеристики, как устойчивость к коррозии, долговечность и простоту ухода.
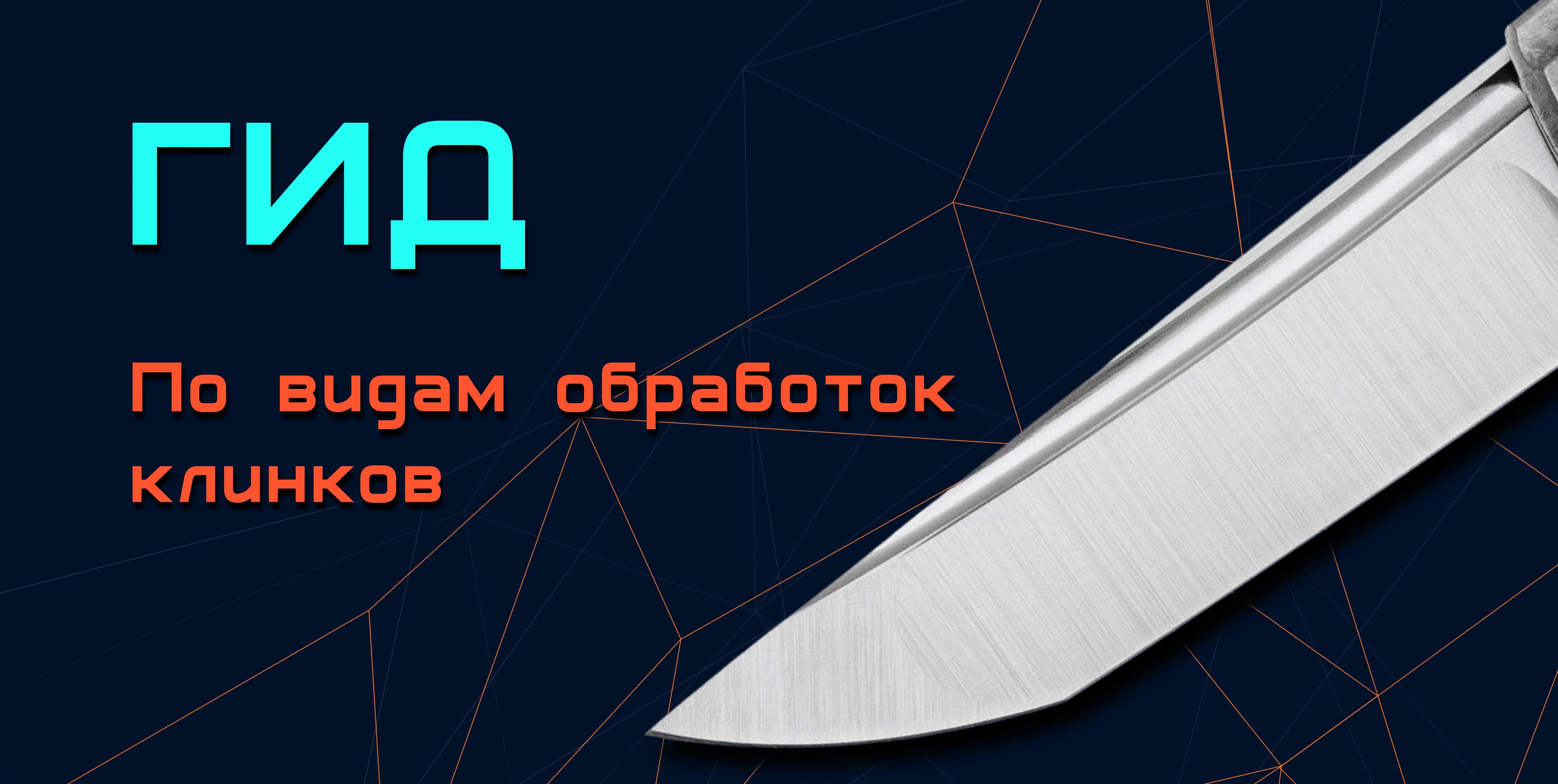
В этой статье мы рассмотрим различные виды обработки клинков, чтобы помочь вам выбрать идеальный нож для дома или активного отдыха. Независимо от того, ищете ли вы инструмент для кухни, туризма или коллекционирования, знание этих тонкостей поможет вам сделать осознанный выбор.
Сатиновая обработка
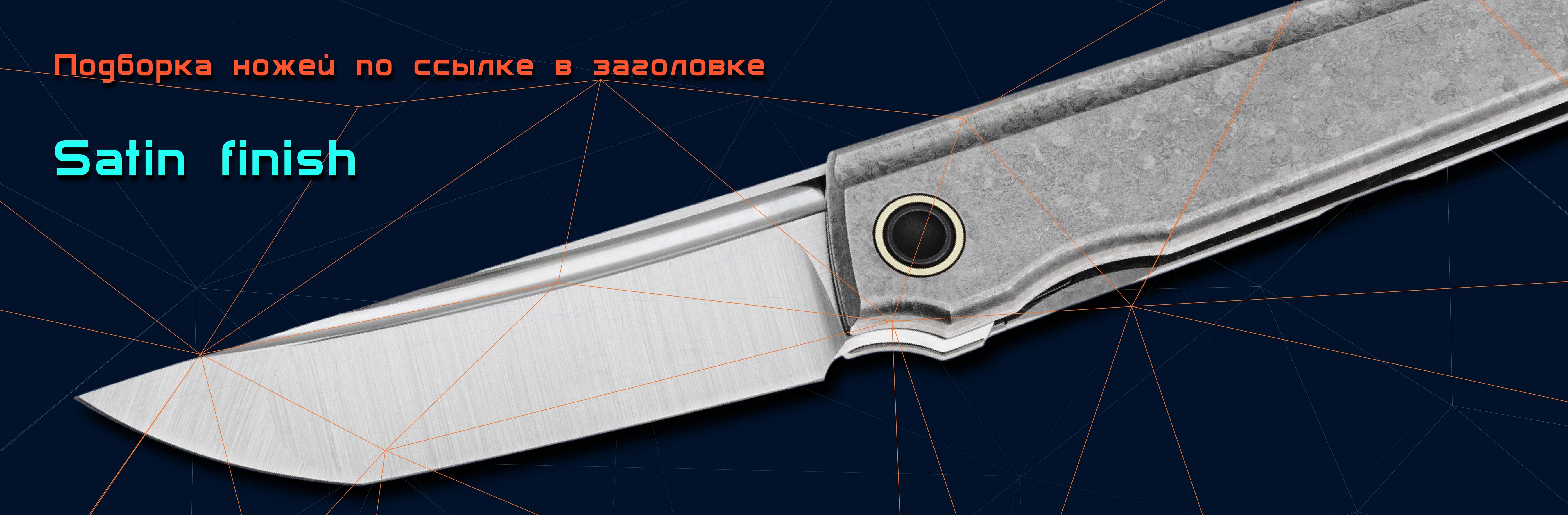
Сатинирование – одна из самых популярных и универсальных видов обработки клинков, которая сочетает в себе эстетическую привлекательность и функциональные преимущества. В процессе сатинирования клинок шлифуется в одном направлении с использованием абразивов разной зернистости, что создаёт ровные, параллельные линии на поверхности. Это придаёт клинку гладкий, матовый вид с мягким блеском, который не отражает свет так сильно, как полированные поверхности.
Виды сатиновой обработки:
- Ручная сатиновая обработка: производится вручную с особым вниманием к деталям, что позволяет добиться более аккуратного и эстетичного результата. Этот метод часто используется на премиальных и коллекционных ножах.
- Машинная сатиновая обработка: выполняется с помощью автоматизированного оборудования. Этот метод позволяет быстрее обрабатывать клинки, но иногда может быть менее точным по сравнению с ручной обработкой.
Преимущества сатинирования:
- Устойчивость к царапинам: сатинирование предоставляет определённую устойчивость к царапинам по сравнению с зеркально полированными поверхностями. Однако важно понимать, что сама по себе сатинированная поверхность не является полностью устойчивой к повреждениям.
- Снижение бликов: сатинирование снижает блики и отражения по сравнению с полированными поверхностями. Это достигается благодаря тому, что сатинированная поверхность имеет менее гладкую текстуру, которая рассеивает свет, вместо того чтобы отражать его прямо.
- Простота ухода: за сатинированными клинками легче ухаживать, чем за зеркально полированными, так как они менее требовательны к чистке и не так сильно показывают следы использования.
- Эстетика: сатинирование придаёт ножу более утончённый и профессиональный вид, что делает его привлекательным для широкого круга пользователей.
Особенности и применения: сатинирование широко используется как на кухонных ножах, так и на охотничьих и тактических моделях. Оно обеспечивает хороший баланс между внешним видом и функциональностью, что делает такие ножи идеальными для повседневного использования.
Обработка Stonewash
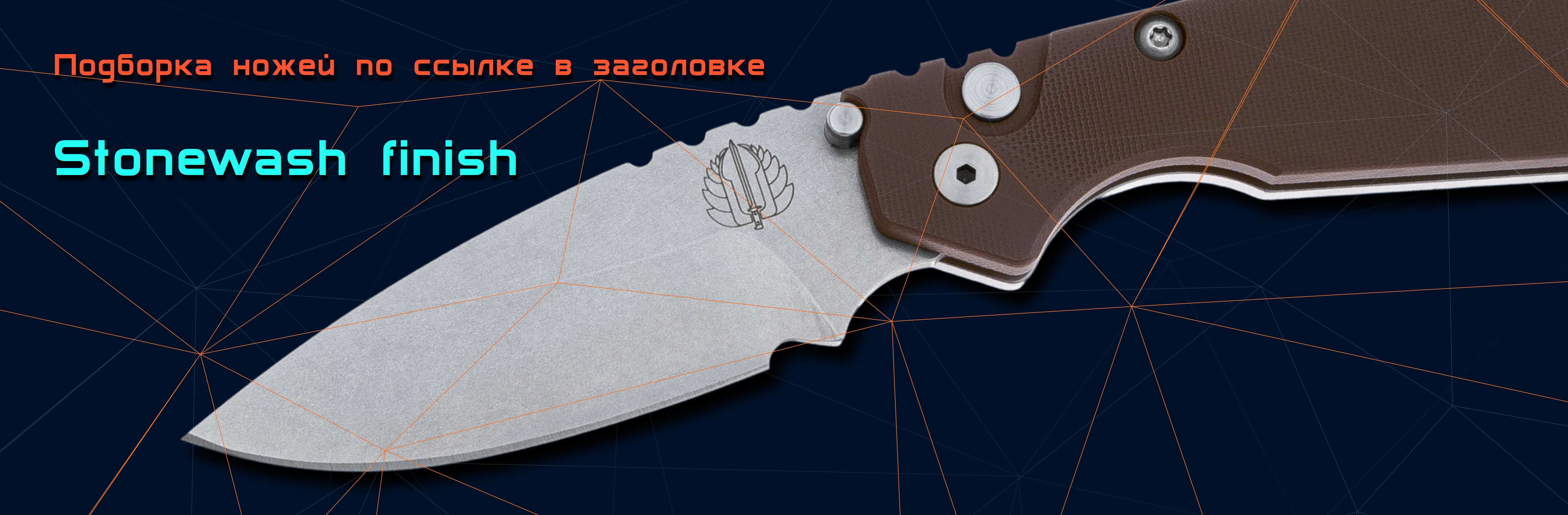
Stonewash – это метод обработки клинков, при котором клинок подвергается воздействию абразивных материалов в барабане, создавая характерную текстурированную и матовую поверхность. Этот процесс придаёт клинку "потертый" вид, который помогает скрывать следы использования и делает ножи с такой обработкой популярными среди тех, кто ценит практичность и долговечность.
Виды обработки Stonewash:
- Обычный Stonewash: клинок подвергается длительному воздействию мелких абразивных камней в барабане, что создаёт равномерную текстурированную поверхность.
- Acid Stonewash (Blackwash): клинок сначала погружается в кислоту для придания ему тёмного, патинированного вида, а затем проходит стандартную обработку Stonewash, что создаёт более контрастный и винтажный вид.
- Heavy Stonewash: клинок подвергается более агрессивной обработке, что приводит к более выраженной текстуре и более заметным потертостям.
Преимущества обработки Stonewash:
- Устойчивость к царапинам: благодаря неровной и текстурированной поверхности клинки с обработкой Stonewash отлично скрывают царапины и мелкие повреждения. Это делает ножи с такой обработкой идеальными для интенсивного использования, так как новые царапины практически незаметны.
- Меньше бликов: матовая текстура Stonewash эффективно снижает блики и отражения света. Это может быть полезно в условиях, где важно минимизировать видимость ножа, например, в тактических или охотничьих ситуациях.
Особенности и применения: обработка Stonewash часто используется на ножах для повседневного ношения (EDC), тактических и охотничьих ножах, а также на ножах для активного отдыха. Она обеспечивает хороший баланс между эстетикой и функциональностью, что делает такие ножи популярными среди широкого круга пользователей.
Обработка Blackwash
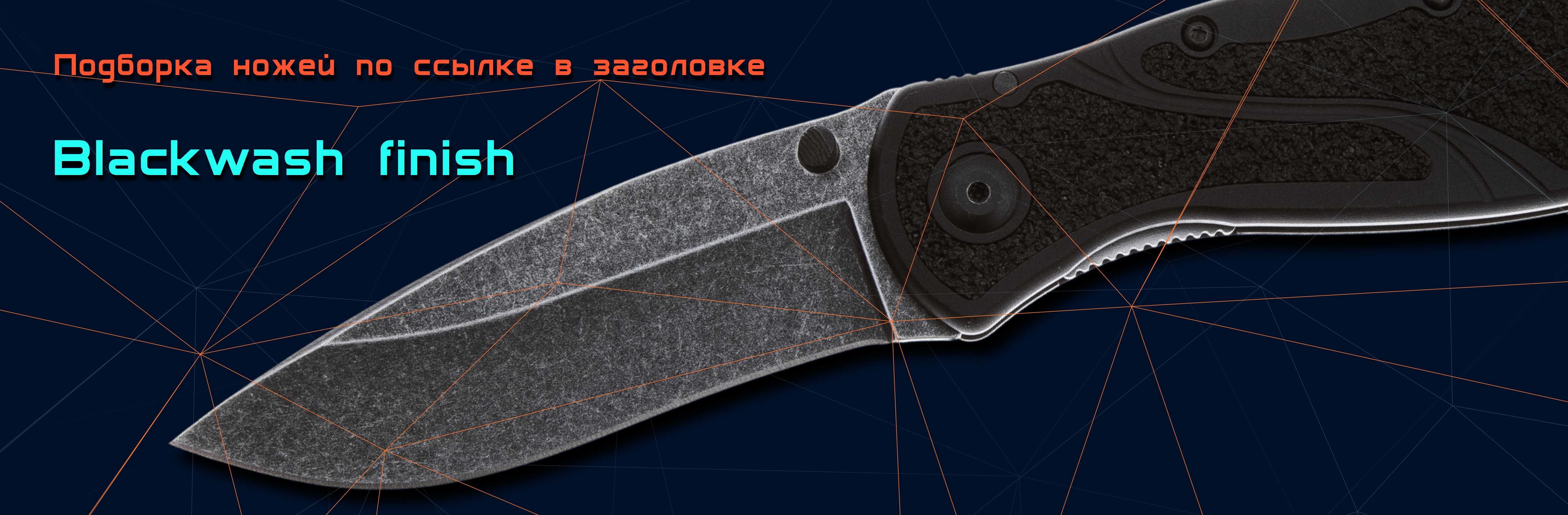
Blackwash – это разновидность обработки клинков, сочетающая два метода: кислотную обработку и Stonewash. В результате получается клинок с тёмным, патинированным финишем и выраженной текстурой, которая создаётся за счёт обработки абразивами. Эта техника обработки придаёт ножам винтажный и агрессивный вид, который особенно популярен среди любителей тактических ножей и инструментов для выживания.
Цвет клинка при обработке Blackwash достигается не только с помощью кислотного травления, но и другими методами:
- Анодирование: хотя чаще применяется на алюминии или титане, может использоваться для придания определённых оттенков или усиления чёрного цвета, полученного в результате травления.
- PVD (Physical Vapor Deposition): этот процесс добавляет сверхтвердое покрытие на поверхность клинка, которое может варьироваться от чёрного до серо-чёрного цвета. Это покрытие не только добавляет цвет, но и улучшает износостойкость и стойкость к коррозии.
- DLC (Diamond-Like Carbon): также применяется для создания стойкого чёрного покрытия. Этот метод обеспечивает высокий уровень защиты клинка, делая его поверхность более твёрдой и устойчивой к механическим повреждениям.
Таким образом, цвет клинка при обработке Blackwash может быть достигнут не только с помощью кислотного травления, но и с использованием других современных методов покрытия, таких как анодирование, PVD и DLC, которые могут усиливать или изменять базовый чёрный цвет клинка и добавлять дополнительные функциональные преимущества.
Обработка Beadblast
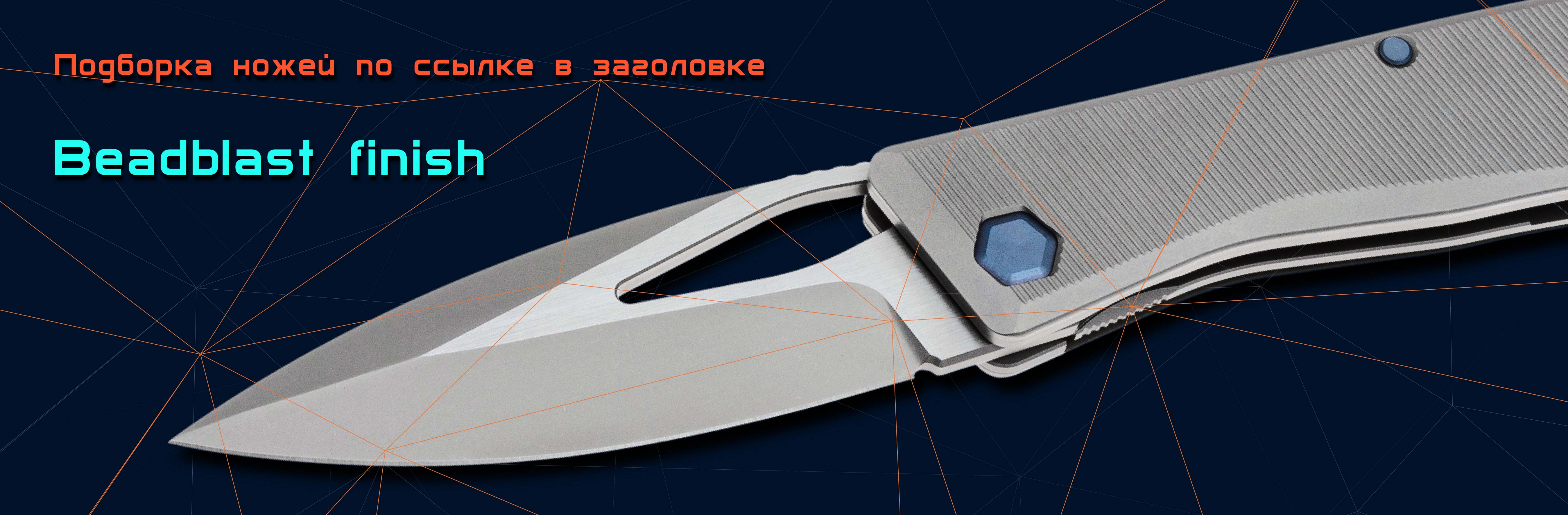
Beadblast – это метод обработки поверхности клинков и других металлических изделий, при котором на поверхность под высоким давлением наносятся мелкие сферические частицы (бисер), обычно из стекла или стали. Эта техника позволяет создавать однородную матовую поверхность с мягким, сатинированным блеском, одновременно очищая и укрепляя материал.
Виды обработки Beadblast:
- Стеклянный бисер (Glass Beads): это наиболее популярный материал для обработки Beadblast, так как он создаёт гладкую, ровную поверхность и может быть использован на различных материалах, включая сталь, алюминий и титан. Стеклянные бисеры разного размера позволяют варьировать степень шероховатости поверхности: от более гладкой до более текстурированной.
- Стальной бисер (Steel Shot): используется для более агрессивной обработки, особенно на твёрдых металлических поверхностях. Стальные бисеры создают более грубую текстуру, что может быть полезно при подготовке поверхности для последующего нанесения покрытия.
- Алюминиевый оксид и карбид кремния: альтернативные абразивы, используемые в случаях, когда требуется более агрессивная обработка или специфическая текстура.
Преимущества обработки Beadblast:
- Однородная поверхность: Beadblast позволяет достичь равномерного покрытия, что особенно важно для декоративных и функциональных изделий. Эта обработка идеально подходит для создания матового финиша с минимальными отражениями света.
- Улучшение адгезии: обработка Beadblast часто используется перед нанесением других покрытий, так как она создаёт поверхность с улучшенной адгезией.
- Удаление дефектов и загрязнений: Beadblast эффективно удаляет ржавчину, окалину и другие загрязнения, улучшая как внешний вид, так и долговечность изделия.
Применение: Beadblast находит широкое применение в различных отраслях, включая аэрокосмическую, автомобильную и медицинскую. На ножах эта обработка часто используется для придания клинку равномерной матовой поверхности, которая устойчива к царапинам и загрязнениям, а также для подготовки клинка к последующей обработке.
Покрытие PVD (Physical Vapor Deposition)
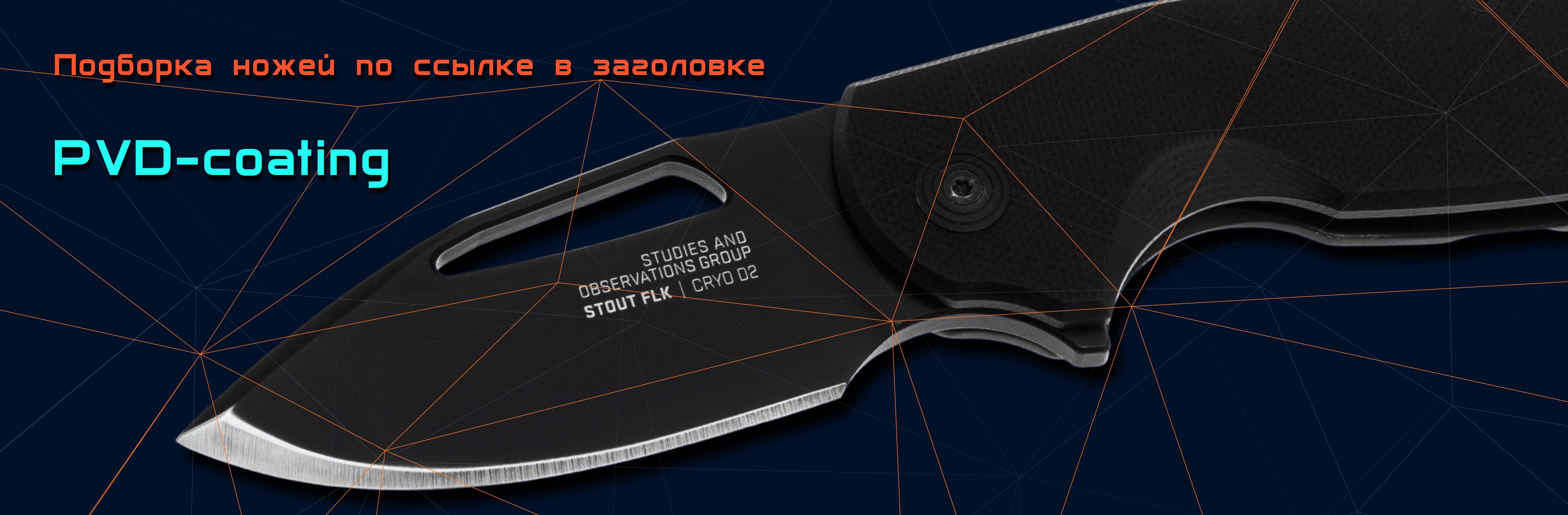
PVD (Physical Vapor Deposition) – это процесс нанесения на поверхность тонкого слоя покрытия путём испарения твердого материала в вакуумной камере и его конденсации на целевой объект. Этот метод широко используется для покрытия ножей, так как он значительно улучшает их эстетические и функциональные свойства.
Виды и материалы PVD-покрытий:
- Titanium Nitride (TiN): одно из наиболее распространённых покрытий, которое обеспечивает высокую устойчивость к износу и коррозии.
- Titanium Carbonitride (TiCN): улучшает твердость и стойкость к истиранию.
- Zirconium Nitride (ZrN): повышает стойкость к коррозии.
- Chromium Nitride (CrN): обеспечивает высокую стойкость к коррозии и износу, часто используется в медицинских инструментах.
Преимущества PVD-покрытий:
- Устойчивость к износу и коррозии: PVD-покрытия обладают высокой твердостью и долговечностью, что делает ножи устойчивыми к повреждениям и коррозии даже при интенсивном использовании.
- Эстетика: PVD-покрытия могут быть выполнены в различных цветах и текстурах, что позволяет создавать уникальный внешний вид ножа. Например, золотистое покрытие из титана не только привлекательно выглядит, но и сохраняет свои свойства на протяжении многих лет.
- Термостойкость: эти покрытия устойчивы к высоким температурам, что особенно полезно для ножей, которые используются в экстремальных условиях.
- Экологичность: в процессе PVD не используются вредные химические вещества, что делает его более безопасным и экологически чистым по сравнению с традиционными методами покрытия.
Применение: PVD-покрытия широко применяются в различных отраслях, включая производство ножей, медицинских инструментов, автомобильных компонентов и даже в электронике. В ножах эти покрытия особенно ценятся за их способность сохранять остроту клинка и предотвращать коррозию, что делает ножи более долговечными и удобными в эксплуатации.
Покрытие DLC (Diamond-Like Carbon) Coating
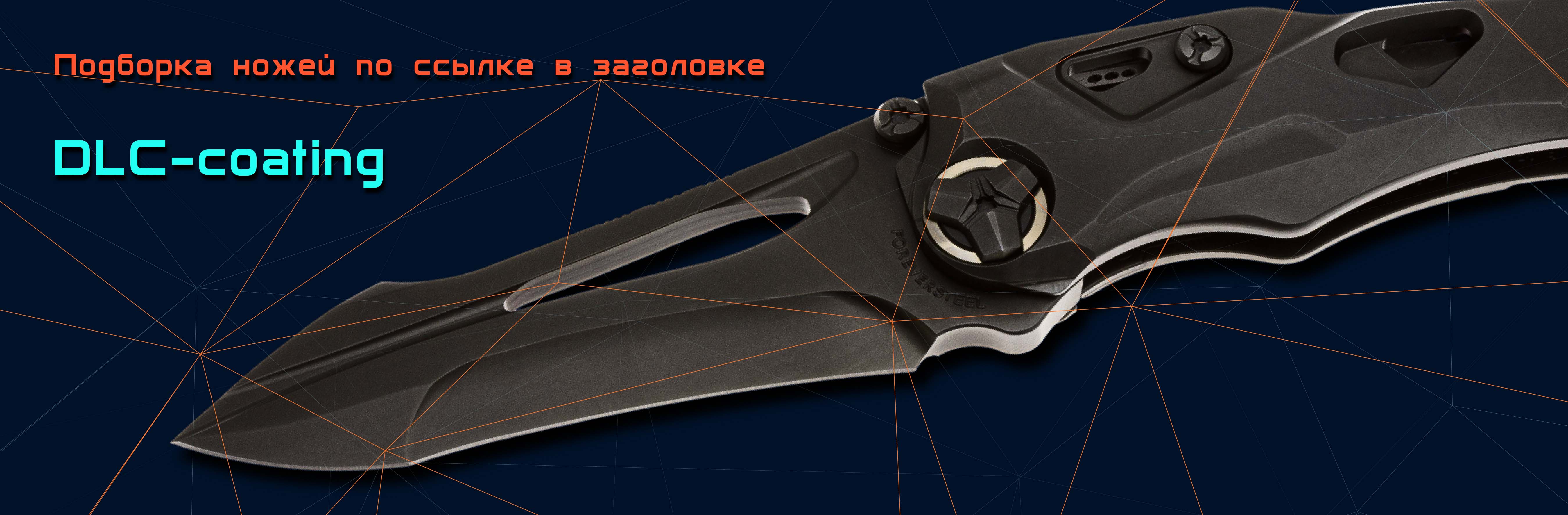
DLC (Diamond-Like Carbon) – это высокоэффективное покрытие, которое сочетает в себе свойства алмаза и углерода. Это аморфное углеродное покрытие, содержащее большое количество sp³-связей, что придаёт ему исключительную твердость, высокую устойчивость к износу и низкий коэффициент трения. DLC-покрытия применяются в различных отраслях, включая производство ножей, автомобилей, медицинского оборудования и электроники.
Виды DLC-покрытий:
- a-C (аморфный углерод): базовый тип DLC-покрытия, состоящий из аморфного углерода. Он не содержит водорода и используется для создания покрытий с умеренной твёрдостью и низким коэффициентом трения.
- a-C (гидрогенизированный аморфный углерод): в этом покрытии углерод комбинируется с водородом. Добавление водорода снижает коэффициент трения, но также может уменьшить твёрдость покрытия по сравнению с другими типами DLC.
- ta-C (тетраэдрический аморфный углерод): один из самых твёрдых типов DLC-покрытий, содержащий высокий процент sp³-связей, что обеспечивает максимальную твёрдость и стойкость к износу.
- ta-C (тетраэдрический аморфный углерод с водородом): этот тип сочетает в себе твёрдость ta-C с добавлением водорода, что может улучшить гибкость покрытия.
- a-C (аморфный углерод с добавлением металла): содержит металлы, такие как титан или хром, что улучшает адгезию покрытия и его устойчивость к коррозии.
Преимущества DLC-покрытий:
- Высокая твёрдость: DLC-покрытия могут достигать твердости до 80 ГПа, что делает их сопоставимыми с алмазами по износостойкости.
- Низкий коэффициент трения: DLC-покрытия обеспечивают очень низкое трение, что улучшает скольжение и снижает износ.
- Устойчивость к коррозии: эти покрытия химически инертны и обеспечивают отличную защиту от коррозии.
- Декоративные свойства: DLC-покрытия имеют привлекательный внешний вид, варьирующийся от антрацитового до глубокого чёрного цвета, что делает их популярными в производстве роскошных товаров, таких как часы и ювелирные изделия.
- Биосовместимость: благодаря своей биосовместимости, DLC-покрытия широко используются в медицинских инструментах и имплантах.
Ограничения:
- Температурные ограничения: DLC начинает терять свои свойства при температуре выше 300°C, что ограничивает его применение в высокотемпературных условиях.
- Стоимость: покрытие DLC дороже, чем другие виды покрытий, что может увеличить общую стоимость изделия.
- Адгезия: DLC может иметь проблемы с адгезией на некоторых подложках, поэтому требуется тщательная подготовка поверхности и использование промежуточных слоёв для улучшения сцепления.
DLC-покрытия используются во многих отраслях благодаря своим исключительным эксплуатационным характеристикам и эстетической привлекательности, что делает их отличным выбором для улучшения долговечности и производительности ножей и других инструментов.
Покрытие Cerakote
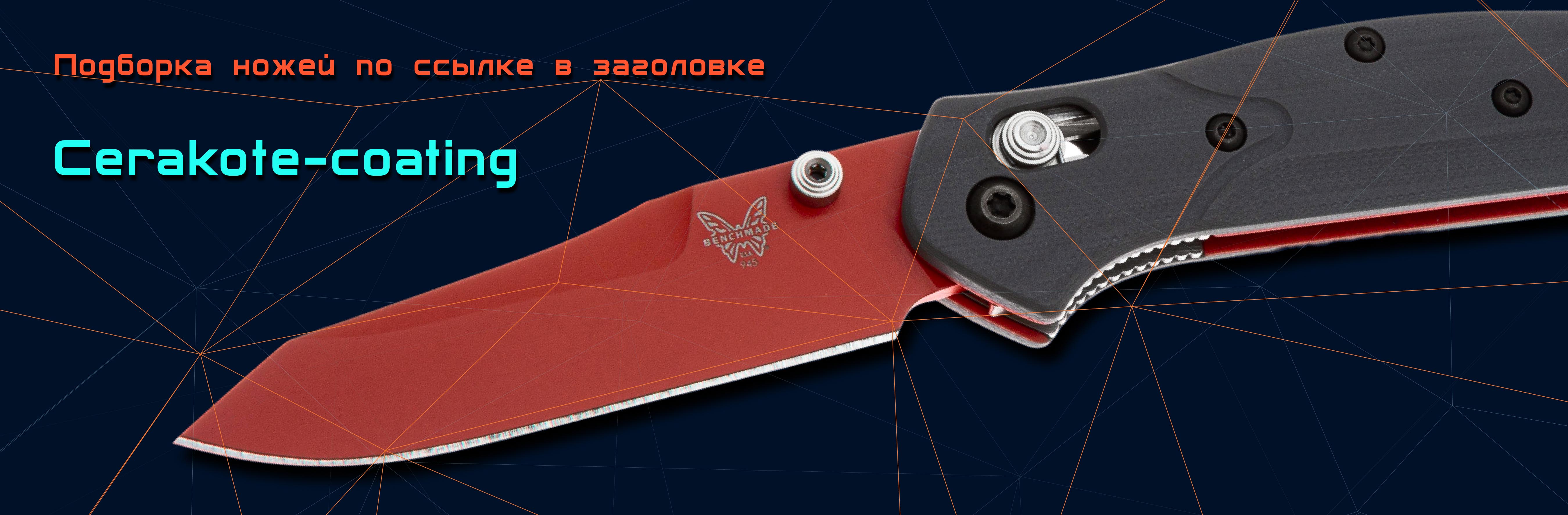
Cerakote – это керамическое покрытие, разработанное для обеспечения превосходной защиты различных материалов, таких как металл, пластик, полимеры и даже дерево. Первоначально разработанное для оружейной промышленности, Cerakote быстро стало популярным покрытием благодаря своей прочности, устойчивости к коррозии и высокой термостойкости.
Преимущества покрытия Cerakote:
- Устойчивость к износу и царапинам: Cerakote демонстрирует отличную стойкость к механическим повреждениям, что делает его идеальным для ножей, оружия и других предметов, подверженных интенсивному использованию.
- Коррозионная стойкость: покрытие защищает материалы от воздействия влаги и химических веществ, предотвращая ржавление и коррозию.
- Термостойкость: Cerakote выдерживает высокие температуры, вплоть до 900°F (около 482°C) для металлов, что делает его отличным выбором для применения в условиях экстремальных температур.
- Разнообразие цветов и визуальная привлекательность: покрытие доступно в широком спектре цветов, которые не тускнеют с течением времени, и может быть использовано для создания как матовых, так и глянцевых текстур.
Применение: Cerakote часто используется для покрытия ножей, огнестрельного оружия, автомобильных деталей, спортивного инвентаря и даже предметов домашнего обихода. Покрытие улучшает внешний вид изделий и одновременно обеспечивает долговечную защиту в экстремальных условиях, будь то жар, химические воздействия или механическое воздействие.
Таким образом, Cerakote является отличным выбором для тех, кто ищет надёжное и долговечное покрытие для своих инструментов и оборудования.
Покрытие EDP (Electro-Deposition Paint)
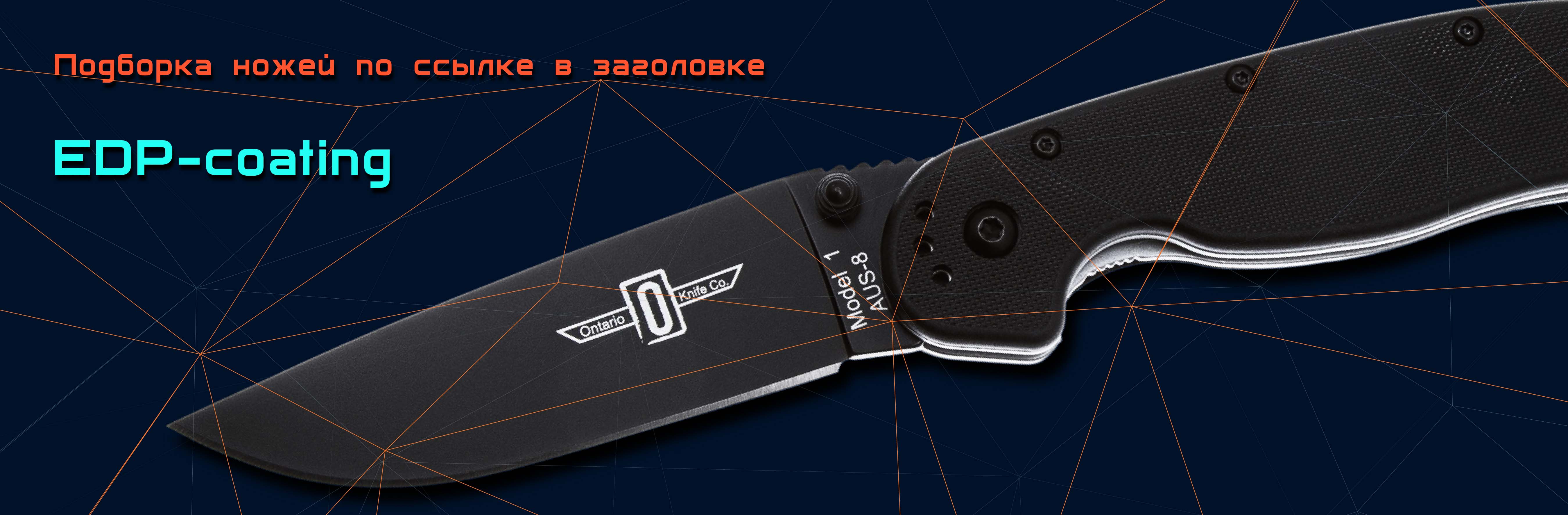
EDP (Electro-Deposition Paint) – это метод покрытия, который применяется для создания тонкого и равномерного слоя краски или лака на металлических поверхностях с использованием электрического тока. Этот процесс обеспечивает отличную защиту от коррозии и других агрессивных воздействий окружающей среды. В промышленности этот метод часто называют "электрофоретическим покрытием" или "электрофоретической окраской" (E-coating).
Виды покрытия EDP:
- EDP Acrylic: покрытие на основе акрила, которое обладает хорошей устойчивостью к ультрафиолетовому излучению и химическим веществам. Этот тип покрытия чаще всего применяется в декоративных и защитных целях.
- EDP Epoxy: эпоксидное покрытие, которое обеспечивает отличную защиту от коррозии и химических воздействий. Оно чаще используется в промышленных и автомобильных применениях, где важна долговечность и стойкость к агрессивным средам.
Преимущества покрытия EDP:
- Универсальность: процесс EDP может применяться для покрытия сложных форм и труднодоступных мест, что обеспечивает полное и равномерное покрытие даже на сложных деталях.
- Устойчивость к коррозии: EDP-покрытия обеспечивают высокую степень защиты от коррозии и окисления, что делает их отличным выбором для изделий, работающих в агрессивных средах.
- Экономичность: покрытие наносится тонким слоем, что делает его экономически выгодным при массовом производстве. Толщина покрытия контролируется путем регулировки напряжения электрического тока.
- Эстетика: покрытия могут быть прозрачными или окрашенными в различные цвета, что позволяет адаптировать их под конкретные требования.
Применение: EDP-покрытия широко применяются в автомобильной, электронной, медицинской и аэрокосмической отраслях. Они используются для покрытия автомобильных деталей, медицинских инструментов, бытовой электроники и спортивного инвентаря, где важны как защита, так и долговечность.
Обработка Black Oxide
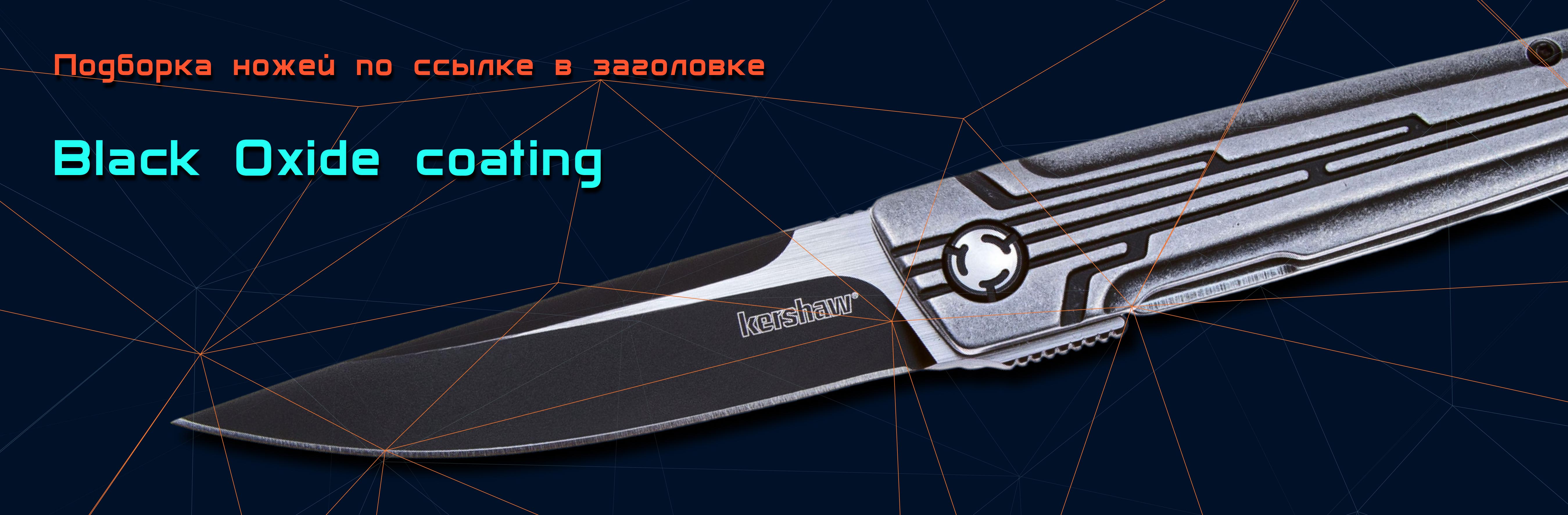
Black Oxide – это процесс химического покрытия, который преобразует поверхность металла в слой чёрного оксида железа (магнетита, Fe₃O₄). Этот тонкий и прочный слой улучшает внешний вид металла, повышает его коррозионную стойкость и уменьшает отражение света. Black Oxide обычно используется на металлических деталях, таких как ножи, оружие, автомобильные и промышленные компоненты.
Виды обработки Black Oxide:
- Hot Black Oxide: самый распространённый метод, при котором металл погружается в горячий щелочной раствор при температуре около 285-305°C. Этот процесс создаёт прочный и устойчивый к коррозии чёрный слой, который широко используется для обработки стальных и нержавеющих деталей.
- Mid-Temperature Black Oxide: аналогичен горячему методу, но проводится при более низких температурах (90-120°C), что снижает вероятность образования токсичных паров. Этот метод даёт более равномерное покрытие и часто применяется в военной промышленности.
- Cold Black Oxide: этот процесс происходит при комнатной температуре (20-30°C) и не требует высокой температуры. Вместо окислительного процесса он наносит на поверхность меди селенид меди, что создаёт чёрный цвет. Однако такое покрытие менее стойкое к износу и обычно используется для декоративных целей или обработки небольших деталей.
Особенности покрытия Black Oxide:
- Коррозионная стойкость: покрытие защищает металл от ржавчины и окисления, особенно при последующей обработке маслом или воском.
- Устойчивость к износу: покрытие Black Oxide обладает умеренной стойкостью к износу, но оно не обеспечивает столь высокой защиты от механических повреждений, как другие виды покрытий, например, PVD или DLC.
- Эстетика: покрытие придаёт металлу насыщенный чёрный цвет, что особенно привлекательно для декоративных и тактических изделий.
- Отсутствие изменения размеров: покрытие не увеличивает толщину деталей, что важно для точных механических компонентов.
Применение: Black Oxide широко используется в производстве ножей, огнестрельного оружия, автомобильных деталей, медицинских инструментов и промышленных машин. Оно улучшает как функциональные, так и эстетические характеристики металлических изделий, делая их более долговечными и устойчивыми к внешним воздействиям. Однако важно учитывать, что чёрный оксид не обладает высокой стойкостью к химическим веществам, поэтому в агрессивных средах может потребоваться дополнительная защита.
Обработка Apocalyptic
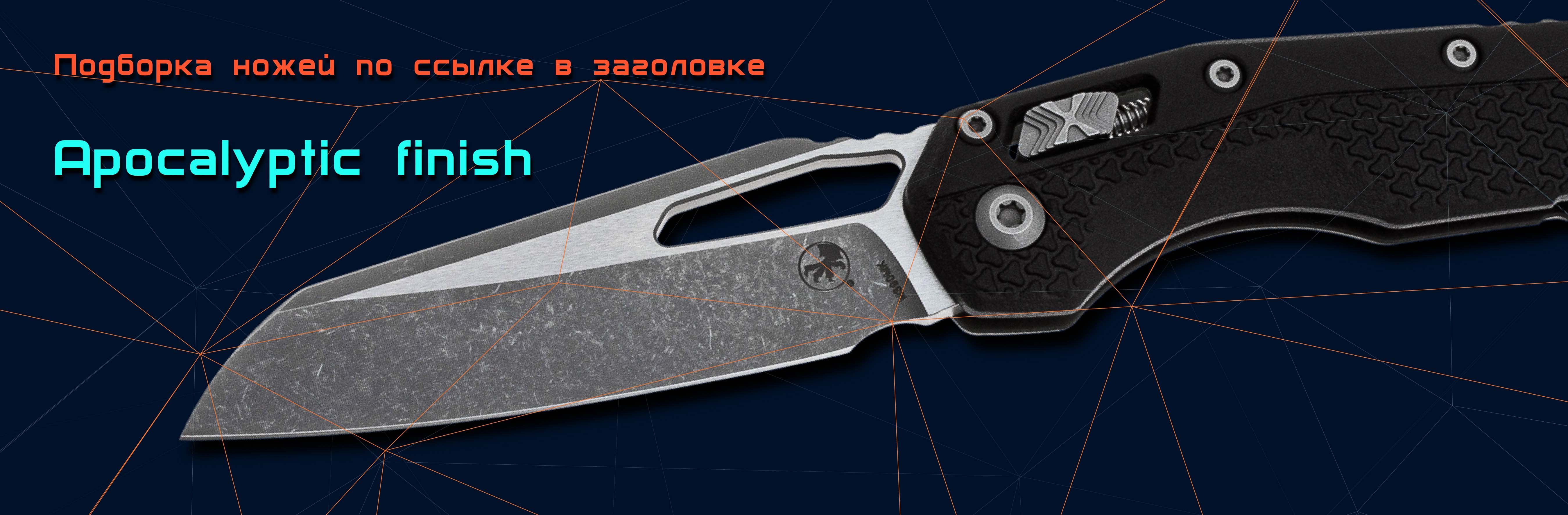
Обработка Apocalyptic – это отделка клинка, которая придаёт ему уникальный, "постапокалиптический" вид, с признаками износа и грубости. Хотя трудно точно указать одного разработчика или создателя этого стиля, он стал популярным благодаря независимым производителям ножей и мастерским, которые стремились создать необычные и характерные отделки для тактических и выживающих ножей.
Основные характеристики и преимущества:
- Эстетика и уникальность: Apocalyptic отделка создаёт впечатление "старения" или "изношенности" клинка, что придаёт ножу особую харизму и отличает его от других. Визуально это часто достигается путём комбинации нескольких методов, таких как Stonewash и кислотное травление, которые вместе создают эффект боевого использования.
- Практичность: благодаря тому, что эта отделка маскирует мелкие царапины и следы использования, ножи с Apocalyptic финишем отлично подходят для тяжёлого и интенсивного использования. Этот финиш делает нож менее подверженным визуальным дефектам в процессе эксплуатации.
- Износостойкость: в отличие от более деликатных финишей, Apocalyptic отделка рассчитана на интенсивное использование. Хотя это не покрытие в традиционном смысле, как PVD или DLC, обработка делает клинок менее восприимчивым к износу благодаря маскировке повреждений и царапин.
Процесс проведения обработки:
- Комбинация методов: Apocalyptic финиш часто достигается путём комбинирования различных методов, таких как Stonewash (обработка камнями), Acid Wash (кислотное травление) и иногда добавления ручных патинирующих техник. Это создаёт на клинке неоднородные текстуры и цвета, которые напоминают следы сильного износа или старения.
- Травление кислотой: часто используется для придания поверхности клинка грубой и матовой текстуры. Этот процесс включает погружение клинка в кислотный раствор, который частично разъедает поверхность, создавая эффект "потрепанности".
- Stonewash: после кислотного травления клинок может подвергаться обработке камнями, что усиливает эффект изношенности. Это делает поверхность более устойчивой к появлению новых царапин и потертостей, так как они органично вписываются в общий вид.
- Ручная отделка: на финальных стадиях некоторые мастера добавляют индивидуальные элементы вручную, чтобы каждый нож был уникальным. Это может включать дополнительные обработки краёв или нанесение особых узоров.
Этот тип отделки используется многими производителями, в том числе Microtech и TRC Knives, которые делают акцент на тактических ножах и ножах для выживания. Визуальный эффект Apocalyptic стал востребованным среди коллекционеров и пользователей, ценящих индивидуальность и практичность в экстремальных условиях.
Заключение
В мире ножей, где каждая деталь имеет значение, выбор финишной обработки клинка – это не просто вопрос стиля, но и практичности. От сатинового блеска до грубого Apocalyptic финиша – каждая обработка предлагает уникальные преимущества, которые могут значительно повлиять на долговечность, внешний вид и функциональность вашего ножа. Понимание различных типов покрытий и обработок поможет вам сделать осознанный выбор, соответствующий вашим потребностям и предпочтениям.
Если у вас есть опыт использования ножей с различными типами обработок или вы хотите узнать больше о конкретных методах, приглашаем вас оставить комментарии. Ваши мнения и вопросы помогут сделать наше обсуждение ещё более интересным и полезным для всех!
0 комментариев